Okay, let me walk you through this sulphuric acid pump situation I dealt with recently. It wasn’t anything too crazy, but required some careful handling, as you’d expect with this kind of stuff.

So, the old pump on our sulphuric acid line started acting funny. The flow wasn’t steady, sometimes it seemed weak, other times it pulsed a bit. Plus, I thought I saw some wetness around the base, which is never a good sign with concentrated acid, right? Didn’t want to ignore that.
Getting Hands-On
First things first, safety gear was essential. Full face shield, heavy-duty chemical gloves, rubber apron, the works. You absolutely cannot mess around with sulphuric acid. One splash and you’re having a really bad day.
Next step was isolating the pump. I shut off the valves on the intake and discharge sides, made sure the line was depressurized, and then carefully drained the pump casing and the immediate pipework into a suitable container. Even then, you assume there’s still some residual acid lurking, so caution is key.
- Shut down the system.
- Put on all the protective gear.
- Isolate the pump section using valves.
- Safely drain the pump and nearby pipes.
With the area safe, I could get a closer look. It was a mag-drive pump, which are usually pretty reliable for nasty chemicals because they don’t have traditional shaft seals that can leak. But even these aren’t totally bulletproof. I cleaned off the outside carefully and confirmed there was definitely some residue near the casing split line. Looked like a seep rather than a major leak, but it needed fixing.
Finding the Problem
Time to open it up. I disconnected the power supply first – always do that. Then I carefully unbolted the casing. Took my time, loosened the bolts evenly to avoid warping anything. Inside, things looked… well, used. The impeller had some minor wear, but nothing looked immediately catastrophic.
The main suspect was the casing O-ring. When I got it out, it felt a bit stiff and looked slightly chewed up in one spot. My guess is that over time, the acid just degraded the material, even though it was supposed to be chemically resistant. Maybe it was just old, maybe the concentration was slightly higher sometimes, who knows. That seemed like our leaky culprit.
The Fix and Finish
Luckily, we keep spares for critical pumps like this. I found the correct seal kit – making sure it was the right material spec for concentrated sulphuric acid is vital. You can’t just slap any old O-ring in there. Cleaned the groove meticulously where the O-ring sits. Any speck of dirt could cause issues.
While I had it apart, I decided to pop in a new impeller too. Seemed silly not to since the pump was already open and we had one on the shelf. Put the new O-ring in place, carefully reassembled the casing, making sure everything lined up perfectly. Tightened the bolts in a star pattern, bit by bit, to ensure even pressure on the seal.
Hooked everything back up – pipes first, then power. Before introducing the acid again, I did a quick test run with water just to check for obvious leaks around the casing seal. Everything looked dry and tight. Okay, good to go.
Slowly opened the isolation valves, letting the acid back into the pump. I watched it like a hawk for the first hour or so of operation. Success! No leaks, and the flow seemed much smoother and more consistent.
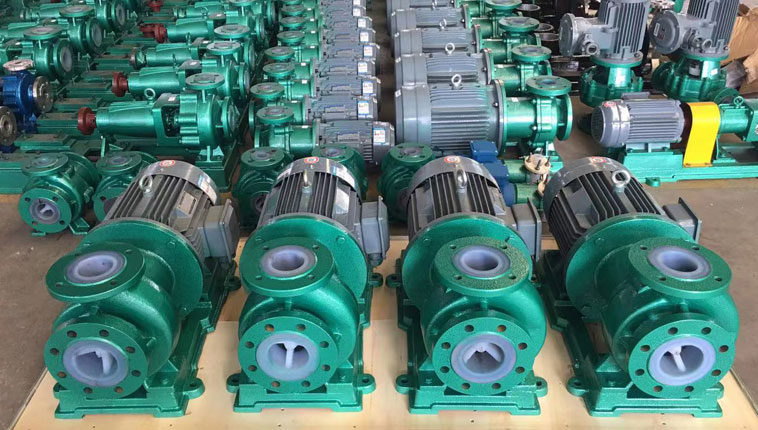
So yeah, that was the adventure with the sulphuric acid pump. Turned out to be just a worn O-ring mainly, but the process requires you to be methodical and super careful. Always respect the chemicals you’re working with. Got it sorted without needing a whole new expensive pump, which is always a good result.