Alright, let me tell you about that magnetic drive pump troubleshooting I tackled last week. It was a bit of a headache, but hey, that’s what keeps things interesting, right?
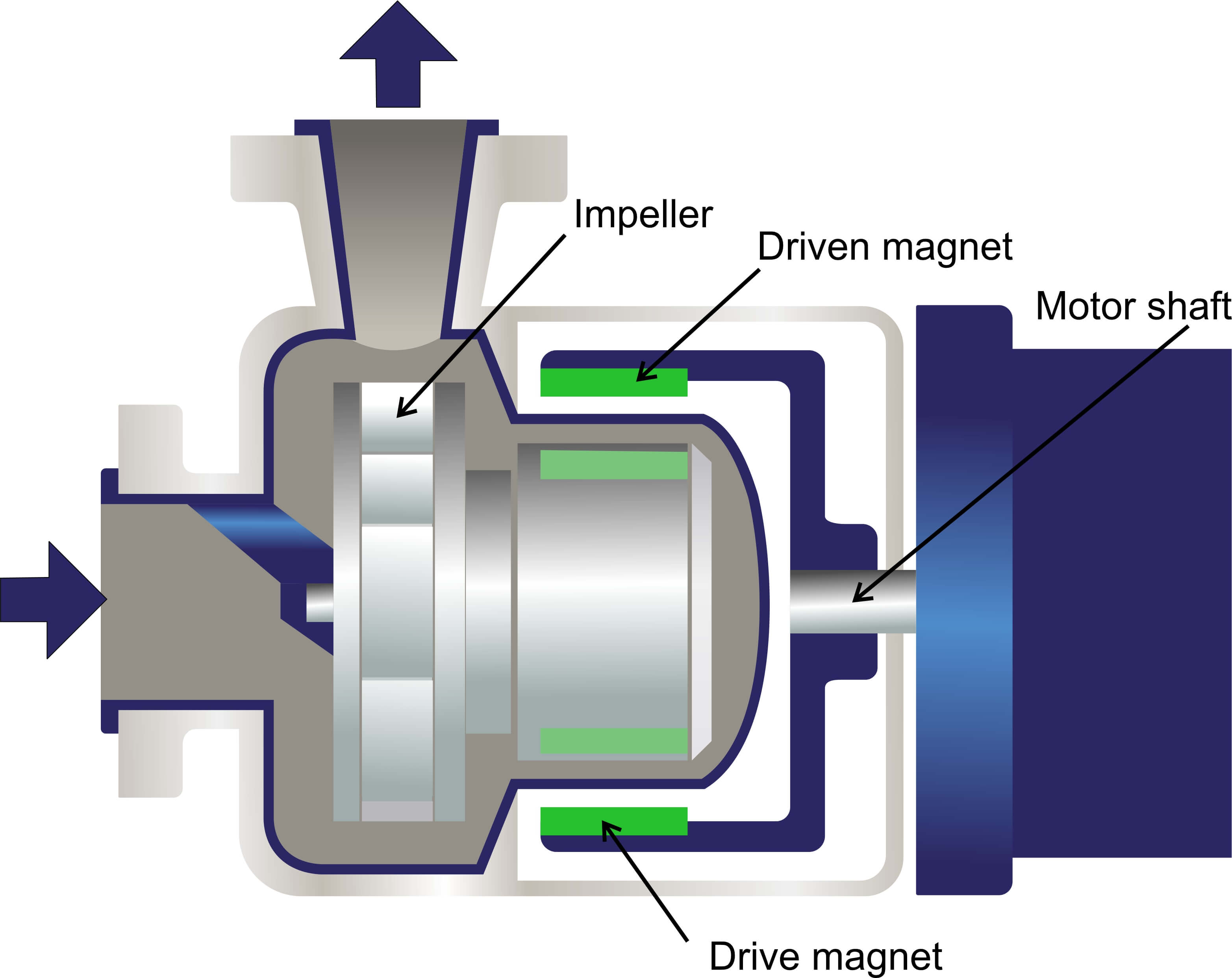
The Problem Starts
So, it all kicked off when the operators noticed the pump wasn’t pumping fluid like it should. Flow rate was way down, and it was making this weird, almost grinding noise. Immediately, red flags went up. Magnetic drive pumps are usually pretty reliable, so when they start acting up, it’s generally a sign of something serious.
First Things First: Safety Check
Before even thinking about touching the pump, I made sure everything was electrically isolated and that the system was depressurized. You gotta be careful with this stuff – safety first, always! Double-checked everything, tagged it out, the whole nine yards.
External Inspection Time
Next, I gave the pump a good once-over from the outside. Looked for any obvious leaks, cracks, or signs of physical damage. Nothing jumped out, which meant the problem was likely internal. Bummer.
Checking the Obvious Suspects
I started with the easy stuff. Checked the motor coupling – making sure it was properly aligned and not slipping. That seemed fine. Then, I verified the power supply to the motor. Voltage was good, no tripped breakers. Okay, so the motor itself was probably okay. Rule those out first.
Time to Get Our Hands Dirty: Disassembly
Alright, deep breath, time to take this thing apart. Slowly and methodically, I started disconnecting the pump from the piping. Made sure to label everything so I could put it back together correctly later (trust me, you’ll thank yourself for this). Once the pump was free, I moved it to the workshop for a proper teardown.
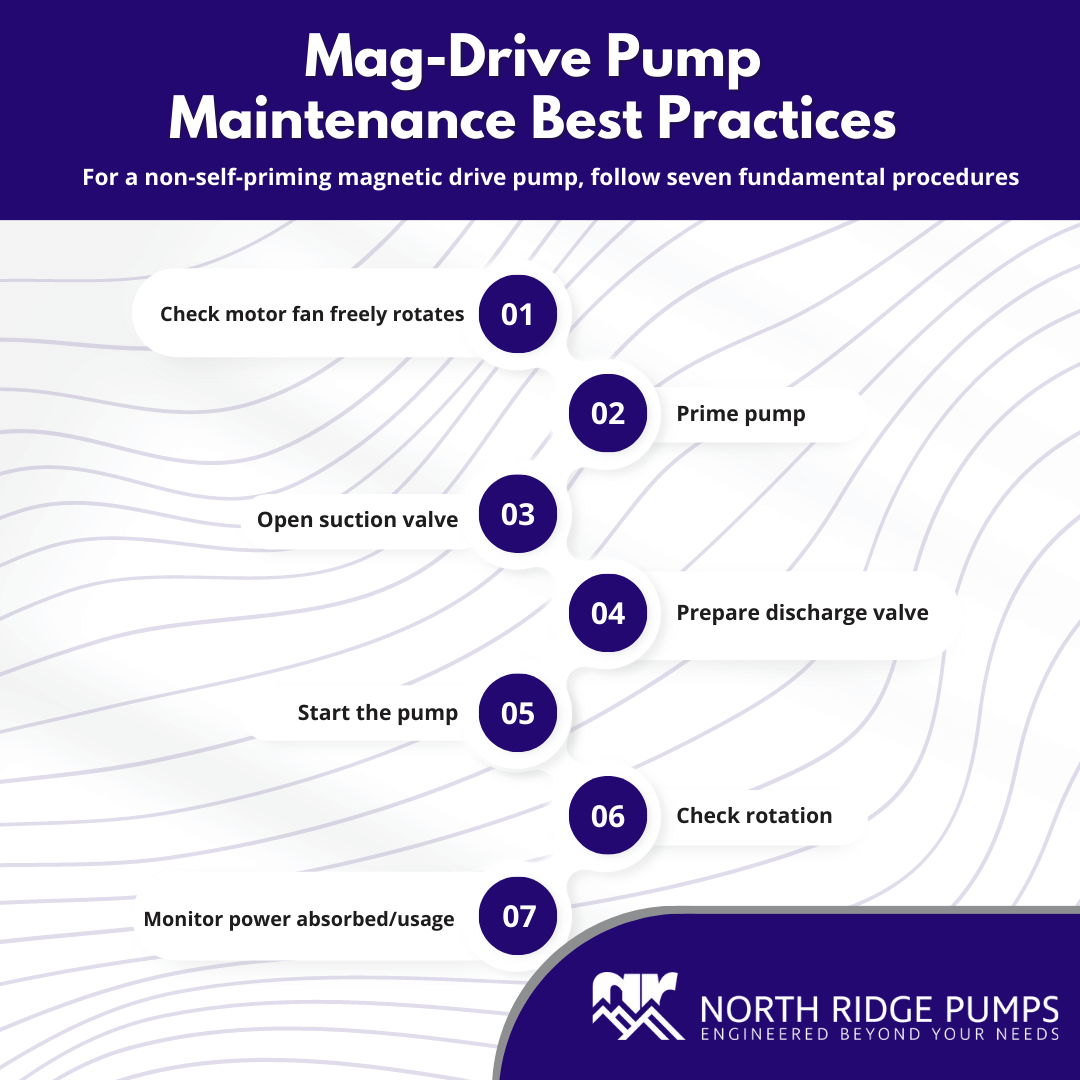
Inside the Beast: The Inspection
With the pump disassembled, the real fun began. I focused on these key areas:
- Impeller: Checked for wear, damage, or obstructions. Looked closely at the impeller vanes for any signs of erosion or corrosion.
- Magnets: This is where things got interesting. One of the magnets on the inner rotor was cracked and chipped! Bingo! That was definitely the source of the grinding noise and reduced flow.
- Bearings: Spun the bearings by hand. They felt rough and gritty. Definitely needed replacing.
- Wear Rings: These were worn down pretty good. Significant clearance increase.
The Root Cause: Figuring Out Why
Okay, so we found the problems, but why did they happen? After looking at the system records and talking with the operators, we figured out that the pump had been running dry for short periods occasionally. This caused the bearings to overheat, which in turn put stress on the magnets and caused them to crack. The worn wear rings probably contributed to the problem as well by allowing more vibration.
The Fix: Replacement and Repair
Here’s what we did:
- Replaced the inner rotor assembly (since the magnets were damaged).
- Replaced all the bearings.
- Replaced the wear rings.
- Thoroughly cleaned all the pump components.
Reassembly and Testing
Carefully reassembled the pump, making sure everything was torqued to the correct specifications. Double-checked all connections. Then, reinstalled the pump in the system.
Before putting the pump back in full service, we ran it through a series of tests. Checked the flow rate, pressure, and vibration levels. Everything looked good! The grinding noise was gone, and the pump was performing like new.
Lessons Learned
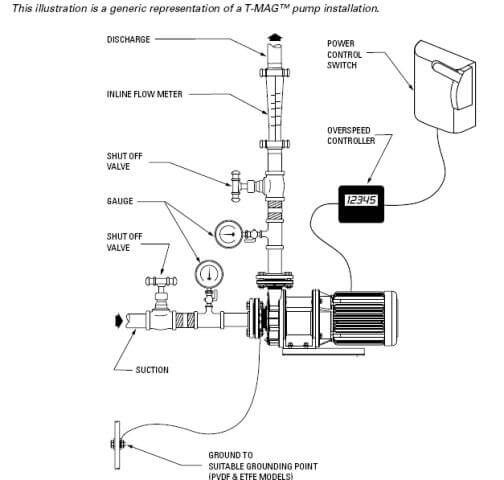
This whole experience highlighted the importance of:
- Regular pump maintenance and inspections. Catching wear and tear early can prevent major failures.
- Preventing dry running. This is a killer for magnetic drive pumps.
- Paying attention to unusual noises or changes in performance. These are often early warning signs of a problem.
Final Thoughts
Yeah, magnetic drive pump troubleshooting can be a pain, but it’s also pretty satisfying when you finally nail down the problem and get things running smoothly again. Hope this helps if you ever find yourself in a similar situation!