Alright, buckle up, because I’m about to spill the beans on my acid centrifugal pump project. It was a wild ride, let me tell you!
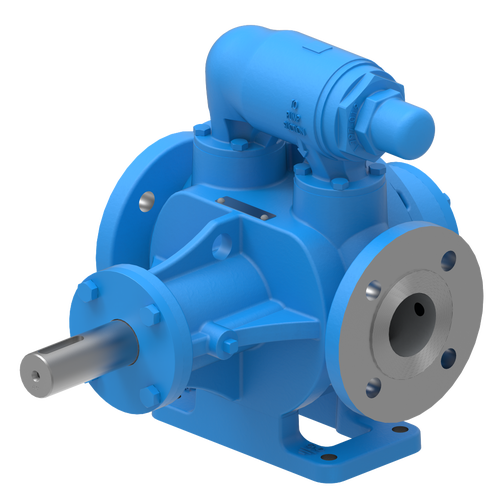
So, it all started when I was tasked with, you know, pumping some seriously corrosive stuff. Standard pumps? Forget about it. They’d melt faster than ice cream on a summer day. That’s when the acid centrifugal pump came into the picture.
First things first: Research! I dove headfirst into a pile of manuals, articles, and anything else I could get my hands on. I needed to understand the beast inside and out. What materials could withstand the acid? How do I size the pump correctly? What kind of seals are needed to prevent leaks that could, well, dissolve everything around?
Next up was sourcing the parts. This wasn’t like grabbing bolts from the local hardware store. We’re talking about specialized alloys, chemical-resistant polymers, and gaskets that could hold their own against a literal acid bath. Finding reliable suppliers who knew their stuff was crucial.
Assembly time! This is where things got interesting. I’m not gonna lie, there were moments where I felt like I was assembling a spaceship. Every bolt, every connection had to be perfect. One wrong move and boom! Acid everywhere. We took our time, double-checked everything, and made sure every seal was airtight (or rather, acid-tight).
Testing, testing, 1, 2, 3. This was the moment of truth. We started with water, just to make sure the pump actually worked without any catastrophic failures. Then, gradually, we introduced diluted acid, carefully monitoring for any signs of leaks, corrosion, or weird noises. It was nerve-wracking, but also super satisfying when it all worked.
Of course, no project is complete without a few hiccups. We had a small leak at one of the flange connections early on. Turns out, we hadn’t torqued the bolts down enough. Easy fix, but it was a good reminder that attention to detail is key.
Here’s a quick rundown of the key takeaways:
- Material selection is everything. Don’t skimp on the right alloys and polymers. Your life (and everything around you) depends on it.
- Proper sizing is crucial. Too small, and the pump will struggle. Too big, and you’re wasting energy and money.
- Seals are your best friend. Invest in high-quality seals and make sure they’re installed correctly.
- Test, test, test. Don’t just assume it’ll work. Start with water, gradually introduce the acid, and monitor everything closely.
Overall, the acid centrifugal pump project was a challenging but rewarding experience. I learned a ton about fluid dynamics, material science, and the importance of following procedures. And hey, I got to play with some pretty cool (and dangerous) chemicals. What’s not to love?