Okay, so I’ve been messing around with these industrial chemical pumps lately, and let me tell you, it’s been a journey. I wanted to share what I’ve been up to, from start to finish, in case anyone else is diving into this slightly messy, but super interesting, world.
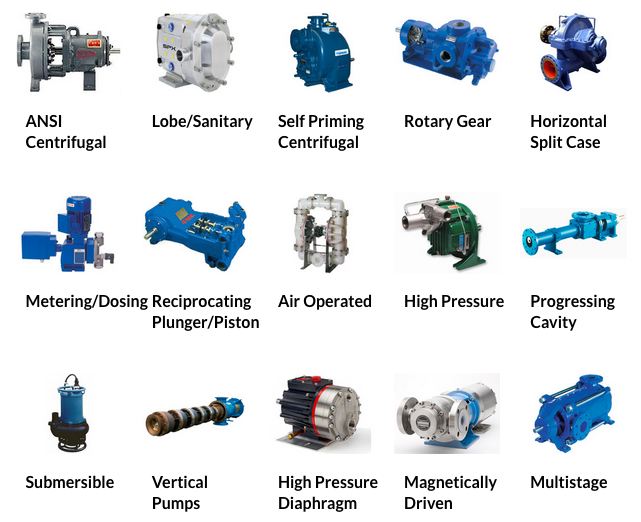
Getting Started: Picking the Right Pump
First things first, I had to figure out which pump to even use. There are so many! I started by making a list of what I needed this pump to actually do.
- What am I pumping? This is a big one. Is it super corrosive? Thick like syrup, or thin like water? Knowing this makes a HUGE difference.
- How much needs to be pumped, and how fast? I’m talking gallons per minute (GPM) or liters, whatever your flavor. You don’t want a tiny pump for a big job, trust me.
- How far does it need to go? This is called “head” in pump-speak. It’s basically the total height difference, plus any friction from the pipes.
- Power source? Do I have easy access to electricity, or am I going to need something air-powered?
After jotting all that down, I began the task to identify the correct one. I decided on a centrifugal pump because I am only pumping water for now.
Installation: It’s Not as Easy as It Looks
Getting the pump was one thing, but getting it installed was a whole other beast. I learned a few things the hard way:
- Level is key! The pump base has to be perfectly level. I spent a good hour shimming it and checking it with a level until it was spot-on. If it’s not level, you’re gonna have problems with vibration and wear.
- Piping matters. I had to make sure all the pipes were properly supported and aligned. Any strain on the pump casing can cause damage. I used a bunch of pipe hangers and made sure everything lined up nice and smooth.
- Suction side is crucial. This is where the pump draws the liquid from. I learned that you need a straight run of pipe before the pump inlet, otherwise, you get turbulence and air bubbles, which is no good.
- Priming is important! You will be needing to fill the pump and the suction line with the chemical before you start it. Otherwise it will just sit there and spin the air.
Testing and Troubleshooting
Once everything was hooked up, I thought I was ready to go. But, of course, there were a few hiccups:
- Weird noises. First time I fired it up, it made this awful grinding sound. Turns out, I had a small piece of debris stuck in the impeller. Had to shut it down, take it apart, and clean it out.
- Low flow rate. The pump was working, but it wasn’t moving the liquid as fast as I expected. I checked all the valves, made sure there were no blockages, and finally realized I had the discharge valve slightly closed. Oops!
- Leaks! Yep, had a couple of small leaks at the pipe connections. Tightened everything up, and that seemed to do the trick. It is important to apply some joint gunk to the threads.
Finally, Sweet Success!
After all the tinkering and troubleshooting, I finally got the pump running smoothly. It’s now moving that chemical like a champ! It was definitely a learning experience, but I’m glad I stuck with it. Now, I feel way more confident tackling any future pump projects. And remember, if a dummy like me can do this, anyone can!