Okay, so let me tell you about this chemical pump situation I tackled recently. It was a bit of a headache, but hey, that’s what makes it fun, right?
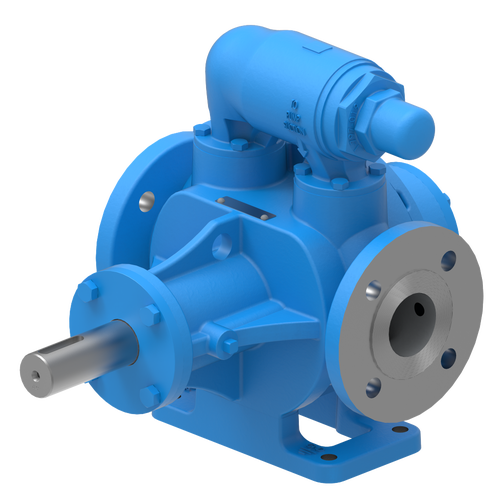
The Problem: We needed a pump that could handle some seriously nasty stuff – acids and corrosive chemicals. Think stuff that eats through metal for breakfast. The existing pump was ancient and leaking like a sieve. Obviously, a new pump was a must, ASAP.
The Research: First things first, I hit the books (well, the internet). I spent a good chunk of time researching different types of chemical pumps. There’s centrifugal pumps, diaphragm pumps, peristaltic pumps… the list goes on. I needed something that was not only corrosion-resistant but also had the right flow rate and pressure for our system. I dug through datasheets, read reviews, and even watched a few YouTube videos (don’t judge!).
Choosing the Right Pump: After what felt like an eternity, I settled on a PTFE (Teflon) diaphragm pump. PTFE is basically impervious to most chemicals, so that was a huge plus. Plus, diaphragm pumps are pretty good at handling abrasive fluids, which was another potential issue. I made sure to calculate the required flow rate and head pressure to get the right size pump. It’s important to over-engineer slightly, just in case.
The Installation: This is where things got interesting. Shutting down the old pump was straightforward enough – just closed the valves and killed the power. But getting the old pump out was a wrestling match. It was rusty, bolted in tight, and generally uncooperative. Lots of WD-40, some grunting, and a few choice words later, it finally came loose.
Next up was installing the new pump. I made sure to use PTFE gaskets and fittings to maintain the chemical resistance. The piping was a bit tricky because the new pump had slightly different dimensions than the old one. I had to do some creative pipefitting to make everything line up. I swear, plumbing is an art form.
Testing and Troubleshooting: With everything connected, it was time for the moment of truth. I slowly opened the valves and switched on the pump. Fingers crossed! Initially, it seemed to work great. But then, I noticed a slight vibration. Turns out, the pump wasn’t properly secured to the floor. A few extra bolts and some rubber dampeners fixed that right up.
Final Thoughts: After a few days of running the new pump, I can confidently say it’s a success. No leaks, consistent flow rate, and no more worrying about corrosive chemicals eating through everything. It was a bit of a challenge, but definitely worth the effort. Now I can check that off the list! Always double check your calculations, and don’t be afraid to ask for help when you’re stuck. And, most importantly, wear the right safety gear!