Okay, so I had this project where I needed to move some pretty nasty chemicals around, and it had to be at a really high pressure. Regular pumps just wouldn’t cut it. That’s when I started looking into high-pressure chemical pumps.
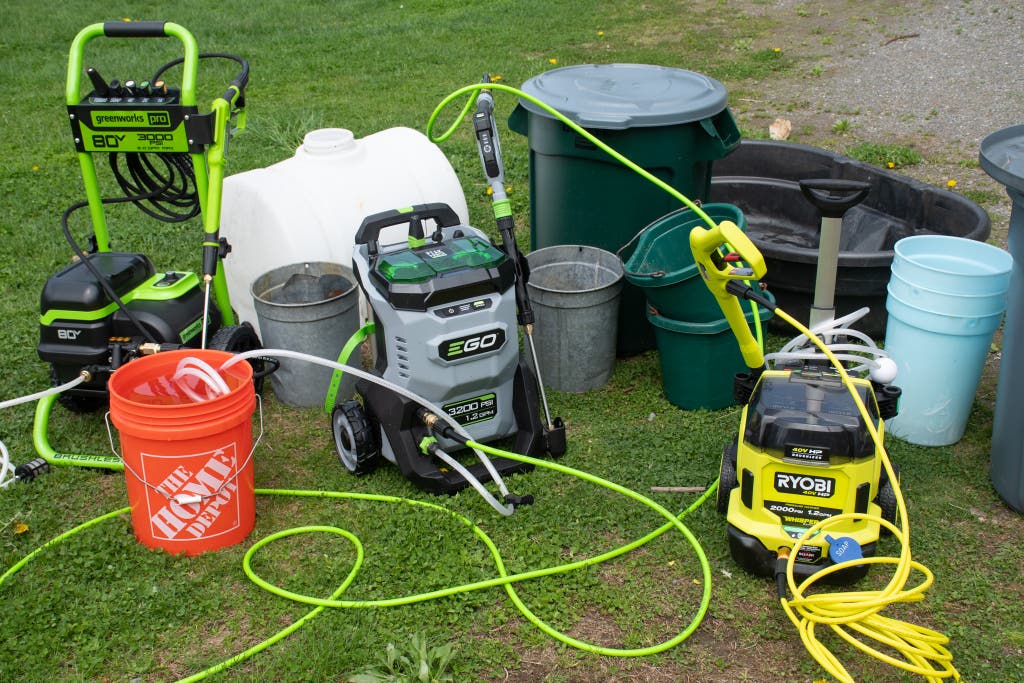
First, I spent a good chunk of time just figuring out what kind of pump I actually needed. There are a bunch of different types, you know? Diaphragm pumps, plunger pumps, piston pumps… it’s a whole world of options. I read a lot of articles and watched some videos. It was like diving headfirst into a pump encyclopedia.
I narrowed it down to a few possibilities based on the chemicals I was using and the pressure I needed. Then, I started reaching out to suppliers. Man, talking to these sales guys is an experience. They all swear their pump is the best, of course.
- Checked the materials: Made sure the pump was compatible with the chemicals. No point in getting a pump that’s going to melt, right?
- Looked at the pressure ratings: Had to be sure it could handle the pressure I needed, with some room to spare. Safety first!
- Considered the flow rate: Needed to move a certain amount of chemical per hour, so the pump had to keep up.
After a lot of back-and-forth, and some serious comparison shopping, I finally settled on a pump. It was a beast of a thing, all stainless steel and heavy-duty seals. And it wasn’t cheap, let me tell you!
Installation Day
Then came the fun part – installation. I cleared out a space in the workshop and got all my tools ready. I followed the manufacturer’s instructions to the letter, triple-checking everything. Bolting it down, connecting the pipes, wiring up the motor…it was a pretty involved process.
Once everything was connected, I did some initial tests with just water. No point in risking a chemical spill if something was wrong. I slowly ramped up the pressure, keeping a close eye on the gauges. It was a bit nerve-wracking, but everything held steady.
Finally, it was time for the real deal. I carefully introduced the chemicals into the system, again starting with low pressure and slowly increasing it. The pump whirred to life, and I could see the chemicals flowing through the sight glass. Success!
I monitored the pump closely for the first few hours, checking for leaks or any unusual vibrations. Everything seemed to be running smoothly. And after several weeks of operation, I can happily say that I pick the right one. It’s been a workhorse, moving those chemicals without a hitch.