Right, let’s talk about this acid pumping unit I wrestled with the other day. It wasn’t anything fancy, just one of those workhorses we’ve had for ages, but boy, it decided to give us a headache.
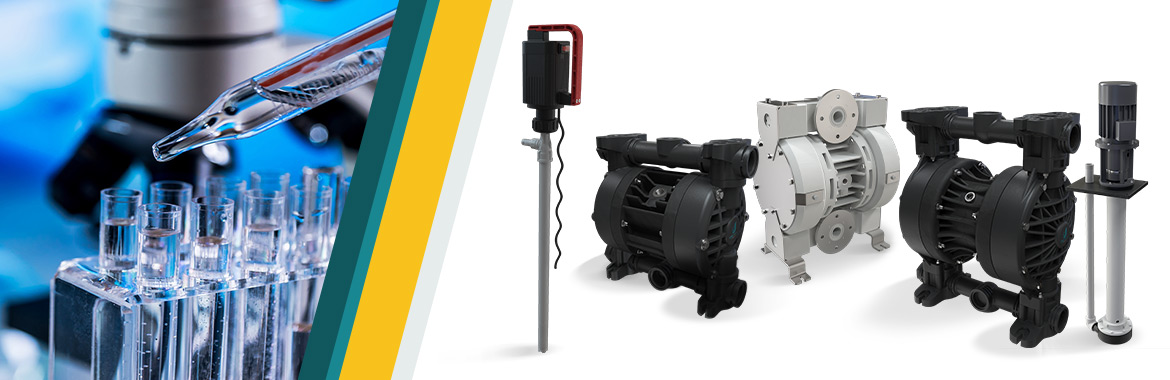
Started the shift, went to get the line running, and nothing. Well, not nothing, more like a sad gurgle. The motor was humming, sounded okay, but no real flow coming out the other end. You know the feeling, right? That sinking feeling ’cause you know your morning’s just gone sideways.
First Checks
So, first things first. I did the usual walk-around. Checked the power, made sure all the breakers were on. Yep, juice was flowing. Listened to the motor again, no weird grinding noises. Okay, motor’s probably fine. Then I looked at the intake side. Was the tank valve open? Yep. Was the line blocked? Gave it a quick check, seemed clear enough.
Moved to the output side. Valve open there too. Followed the pipe a bit, no obvious kinks or leaks. Everything looked… normal. That’s usually when the real fun begins, isn’t it?
Getting Hands Dirty
Alright, time to dig in. Put on the gear – gloves, face shield, the whole nine yards. Dealing with acid, even if it’s just residual, you don’t mess around. I shut everything down, locked it out properly. Safety first, always.
I figured the issue had to be inside the pump housing itself. Maybe the impeller was jammed or something was clogged internally. Getting the housing off these older units can be a real knuckle-buster. The bolts were corroded, naturally. Needed some penetrating oil and a bit of muscle.
Once I got it open, I had a look inside. Here’s what I checked:
- Impeller: Gave it a spin by hand. Seemed to move okay, no obvious obstructions. No broken blades.
- Seals: This is where things got interesting. The main seal looked a bit worn, kinda chewed up on one edge. Could that be it? Maybe it was letting air in, losing the prime?
- Internal passages: Shone a light in there. Found some gunky buildup, but nothing that looked like a complete blockage. Scraped some of it out anyway.
Decided to replace that seal. It looked suspect, and it’s often the culprit with these older pumps. Had to rummage around the workshop to find the right replacement part. Took longer than I care to admit, sorting through boxes of bits and pieces.
Putting it Back Together
Cleaned everything up nicely. Popped the new seal in, making sure it was seated just right. Bolted the housing back on, tightening the bolts evenly, criss-cross pattern, you know the drill. Didn’t want to warp anything or create a leak.
Reconnected the lines, double-checked everything. Took off the lockout tag. Moment of truth.
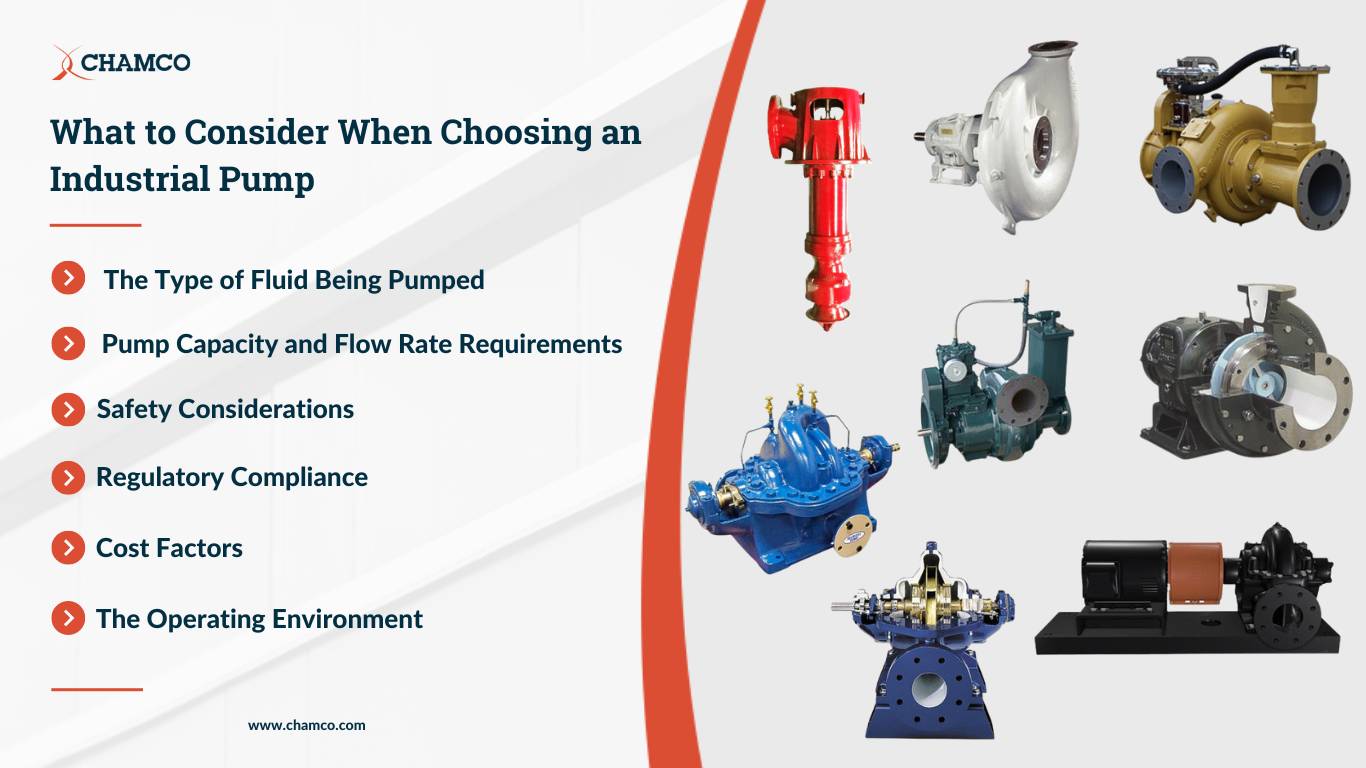
The Result
Opened the valves slowly. Flipped the switch. The motor hummed, then… success! That lovely sound of liquid flowing properly. Watched the flow meter, and yup, we were back in business. Let it run for a good 20 minutes while I kept an eye on it. No leaks, no weird noises. Pressure held steady.
Just goes to show, sometimes it’s the simple things, like a worn seal. But finding it takes time, effort, and getting your hands dirty. Glad that one’s sorted, for now anyway. These old machines, they keep you on your toes.