Alright folks, let’s talk about my acid injection pump project. Been wrestling with this thing for a solid few weeks now, and I figured I’d share the whole messy process, start to finish. Consider this your “don’t do what I did” guide, with a few “maybe do this” sprinkled in.
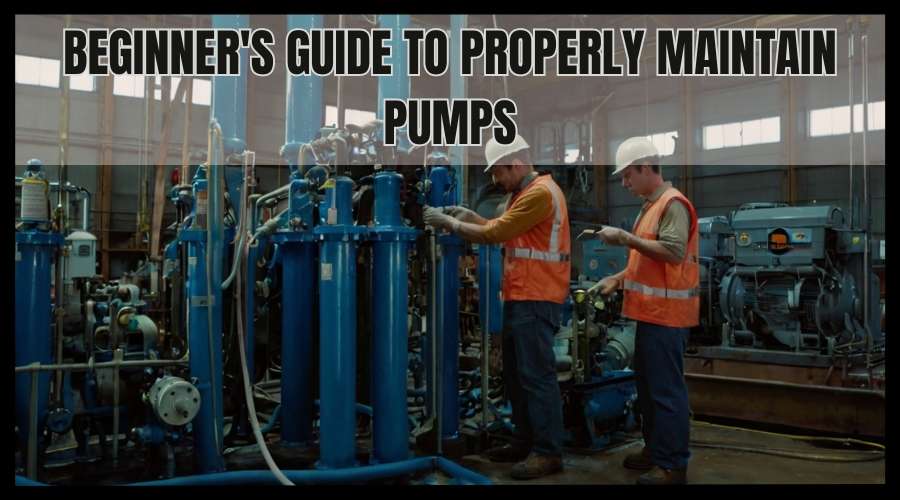
So, background. We’re dealing with some seriously alkaline water in our process, like pH levels that could strip paint. The solution? Acid injection. Simple enough in theory, right? Grab a pump, a tank of acid, and Bob’s your uncle. Wrong.
First things first, I started by researching pumps. Diaphragm pumps, peristaltic pumps, solenoid pumps… my head was spinning. I eventually landed on a diaphragm pump because it seemed robust enough for the job and could handle the corrosive nature of the acid. I ordered a ProMinent Concept Plus pump, based on a recommendation from a buddy who works in water treatment. Seemed legit.
Next up, the acid tank. I sourced a polyethylene tank from a local supplier. Made sure it was rated for the specific acid concentration we were using. Didn’t want any surprises there. I also installed a vent to prevent pressure build-up. Safety first, kids.
Then came the fun part – the plumbing. I laid out the entire system, from the acid tank to the injection point in the main water line. I used schedule 80 PVC pipe and fittings, again for corrosion resistance. I glued everything together (after dry-fitting, of course), and let it cure for a full 24 hours. No leaks allowed.
Now, for the electrical. The pump needed power, and I wanted some basic control. I wired up a simple on/off switch and a variable frequency drive (VFD) to control the pump speed. The VFD was a lifesaver, allowing me to fine-tune the acid injection rate. I also installed a flow meter downstream of the injection point to monitor the flow rate and ensure proper mixing.
Time to test. I filled the acid tank (carefully, with proper PPE!), primed the pump, and turned it on. And… nothing. The pump was making noise, but no acid was flowing. Turns out, the suction line was too long, and the pump couldn’t overcome the head pressure. Doh!
I shortened the suction line and tried again. This time, acid flowed, but it was sputtering and inconsistent. I discovered that there was air trapped in the pump head. I bled the air, and the pump finally started running smoothly. Success!
Not so fast. After a few hours of operation, the pH of the water started to drop too low. The pump was injecting too much acid. I adjusted the VFD to reduce the pump speed, but it was still overshooting. Turns out, the pump’s calibration was off. I had to calibrate the pump using a graduated cylinder and a stopwatch to accurately determine the flow rate at different VFD settings. It was tedious, but necessary.
Finally, after a week of tweaking and adjustments, the system was running smoothly and consistently. The pH was stable, the flow rate was correct, and the pump was operating reliably. I even added a pH controller that automatically adjusts the pump speed based on the downstream pH, making the whole system self-regulating.
So, what did I learn? Here are a few key takeaways:
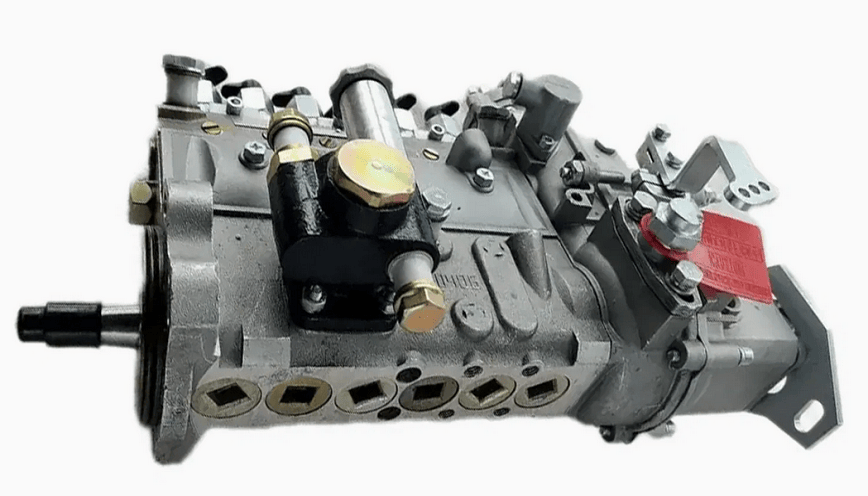
- Research is crucial. Understand the different types of pumps and their capabilities.
- Material selection matters. Use corrosion-resistant materials for all components that come into contact with the acid.
- Proper plumbing is essential. Ensure that all connections are tight and leak-free.
- Electrical safety is paramount. Use proper wiring techniques and grounding.
- Testing and calibration are critical. Don’t assume that the pump is accurate out of the box.
This acid injection pump project was a real pain in the butt, but it was also a valuable learning experience. I hope my mistakes and successes can help you avoid some headaches in your own projects. Good luck!