Okay, so I had this project where I needed a pump that could handle some pretty nasty chemicals. You know, the kind that would eat through regular materials like they were nothing. I did a bit of digging and realized I needed a “chemical resistant pump,” but honestly, I had no idea where to start.
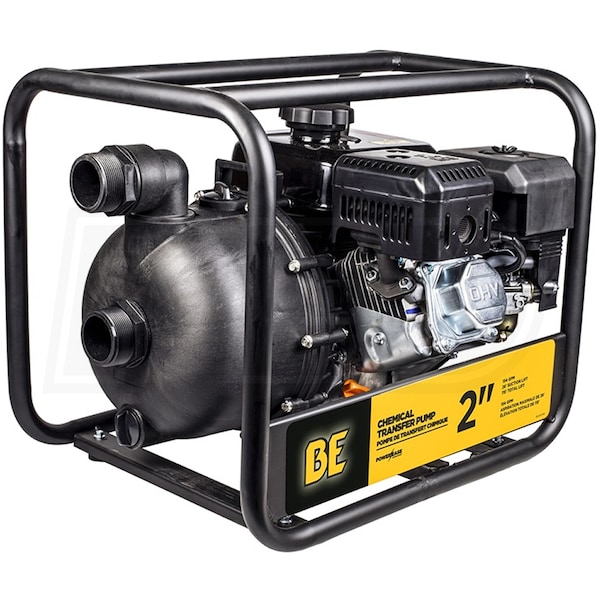
Figuring Out What I Needed
First, I had to figure out exactly what kind of chemicals this pump would be dealing with. I made a list of everything, noting down stuff like concentrations and temperatures. I also looked at how much liquid I needed to move and how fast – the flow rate and pressure, I think they’re called. It’s easy if do some searching.
Choosing the Right Materials
Next up was figuring out the pump materials. This was a bit of a headache. I learned about different types of plastics, like polypropylene and PVDF, and even some fancy metals like Hastelloy. It was all about finding something that wouldn’t react with the chemicals I was using. I spent a good chunk of time reading through compatibility charts – basically, big tables that tell you what materials are okay with what chemicals.
Picking a Pump Type
Then there was the whole issue of choosing the actual pump type. There are tons of different pumps out there! I looked into a few, like:
- Centrifugal pumps: These seemed pretty common and good for moving a lot of liquid.
- Diaphragm pumps: These sounded good for handling really nasty stuff because the liquid doesn’t touch any moving parts.
- Peristaltic pumps: I read that these are super accurate and gentle, which might be good for some applications.
It was a tough choice, but I eventually went with a magnetic drive centrifugal pump. It seemed like a good balance of being able to handle the chemicals and having a decent flow rate. Plus, the magnetic drive meant there were no seals to leak, which was a big bonus.
Getting it Installed
After checking my wallet, I found a supplier who seemed to know their stuff. Ordered that sucker and, it was a whole other adventure, making sure I had the right pipes, fittings, and safety gear. I’m no plumber, but I managed to get everything hooked up without any major disasters and thankfully, it didn’t explode.!
Testing and Keeping it Running
Once everything was connected, I did some test runs with plain water, just to make sure there were no leaks. Then, I slowly introduced the chemicals, keeping a close eye on everything. It all worked out, and the pump has been chugging along ever since.
I also learned that I needed to do some regular maintenance, like checking for wear and tear and replacing parts if needed. It’s not exactly exciting, but it keeps things running smoothly. And if it breaks down, it’s gonna be another huge headache.
So, that’s my story of diving into the world of chemical resistant pumps. It was definitely a learning experience, but I’m pretty happy with how it all turned out.